5S + Relocation = WIN!
The Benefits of Upgrading Your Company Relocation with 5S
Relocations and expansions are tough work. One tool we use to lighten the workload is 56S. More on the 6 later.
5S is a Lean Six Sigma tool that has its roots in lean manufacturing from Japan. It formalizes the old adage of “A place for everything and everything in its place”. The 5Ss stand for:
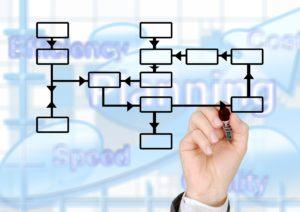
Japanese | Translated | English | Definition |
---|---|---|---|
Seiri | Organize | Sort | Eliminate whatever is not needed by separating needed tools, parts, and instructions from unneeded materials. |
Seiton | Orderliness | Set in order | Organize whatever remains by neatly arranging and identifying parts and tools for ease of use. |
Seiso | Cleanliness | Shine | Clean the work area by conducting a cleanup campaign. |
Seiketsu | Standardize | Standardize | Schedule regular cleaning and maintenance by conducting seiri, seiton, and seiso daily. |
Shitsuke | Discipline | Sustain | Make 5S a way of life by forming the habit of always following the first four S’s. |
© 2019 American Society for Quality
Many Lean and continuous improvement practitioners including us preamble these with a 6th S-Safety! 360° Safety should always be the first consideration in any improvement or relocation project.
This tool can be used to greatly enhance the relocation process. By performing the first 4S’s in the chart just prior to relocation begins, the movement of unused materials is prevented. This can include scrap, obsolete, or superseded parts, broken equipment, or equipment that no longer meets current safety standards. After the new facility is online, maintaining the gains by continuing with 6S processes is a forward looking path.
Additionally, this enables the project team along with the folks on the Geemba (Work Floor) to envision the new work space and start optimizing it. When the actual relocation occurs, the impact of the status quo is lessened and the process is “fresh”, without legacy distractions.
Optimizing during relocation will also have a major impact in achieving the planned ROI. Many organizations have moved into new-larger-better facilities and replicated their old processes and workflows. This just enables the bottlenecks a larger stage to play on. When this happens, the expected ROI is reduced and sometimes it can actually turn negative. This scenario can be avoided by careful planning, employee engagement, and change management.
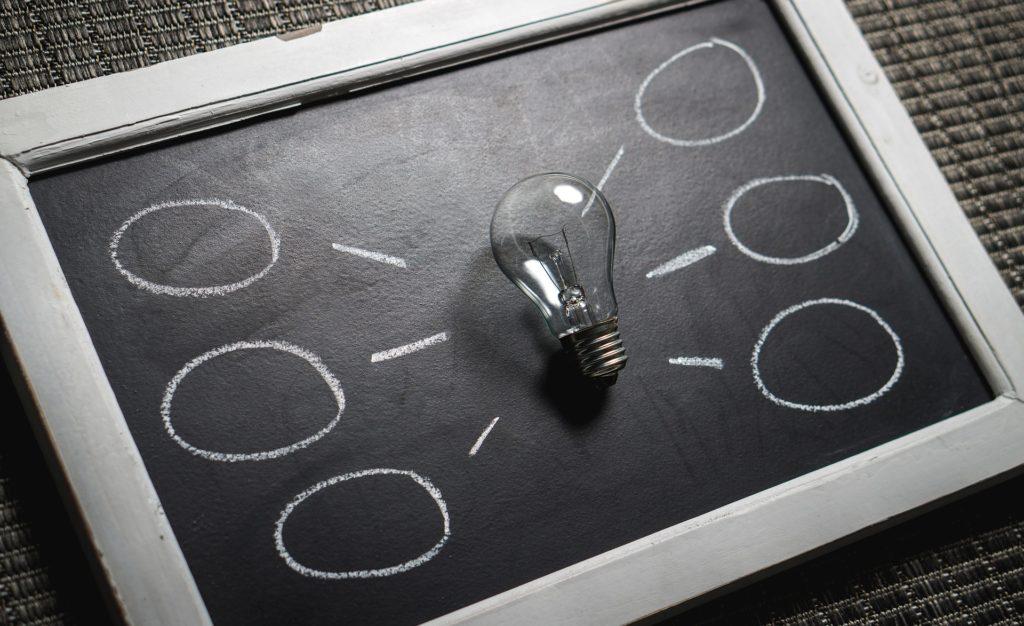